cms electronics
Development
A successful product starts with a good idea. As the creation of technical objects through targeted considerations, experiments and constructions, development is the basis for our society today.
Our development team supports you in realizing your ideas. The extent of this collaboration depends on the product and your wishes. Some of our customers develop electronics themselves down to the smallest detail - others concentrate on the specifications and outsource the development completely.
The proximity of our development to the production environment guarantees the use of optimal manufacturing processes, the shortest possible throughput times and product quality at the highest level right from the start.
New development, further development, design optimization
Development all-inclusive
Our development team covers all relevant areas: project management, circuit and hardware development including layout, software development, construction and design, sample and prototype production as well as durability and environmental testing – and much more.
Whether you need a new development, further development or design optimization – you have come to the right place!
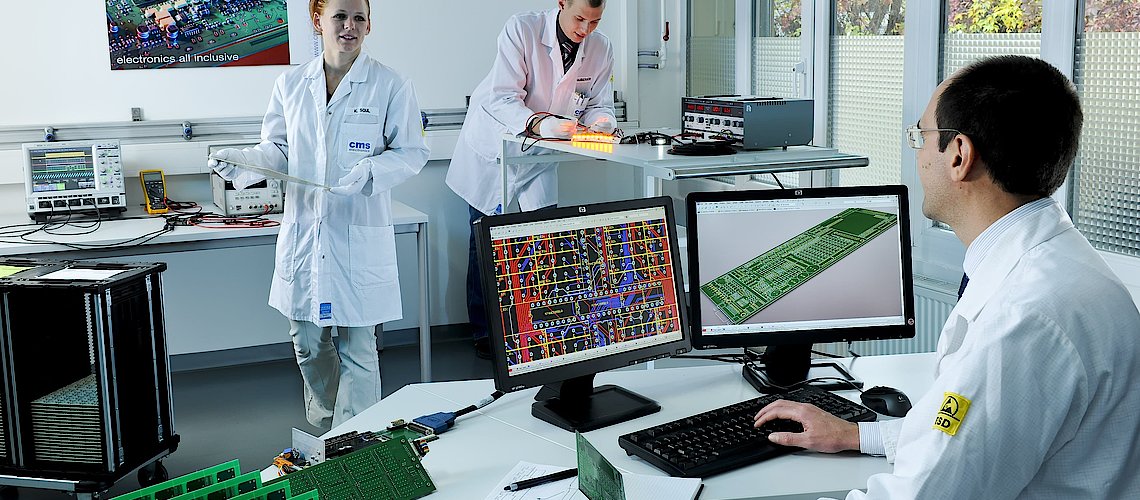
npi
New Product Introduction
In order to create a successful product and to maximize the added value as much as possible, it is important that development and product launch go hand in hand.
From prototype development to the finished series product and the subsequent transfer to series production, the NPI (New Product Introduction) department of cms electronics is jointly responsible for ensuring your product is a complete success.
With the expertise of cms electronics, your electronics will be planned and designed to be production- and cost-optimized, ready for series production. During the entire NPI process, up to 80% of the subsequent production costs are determined.
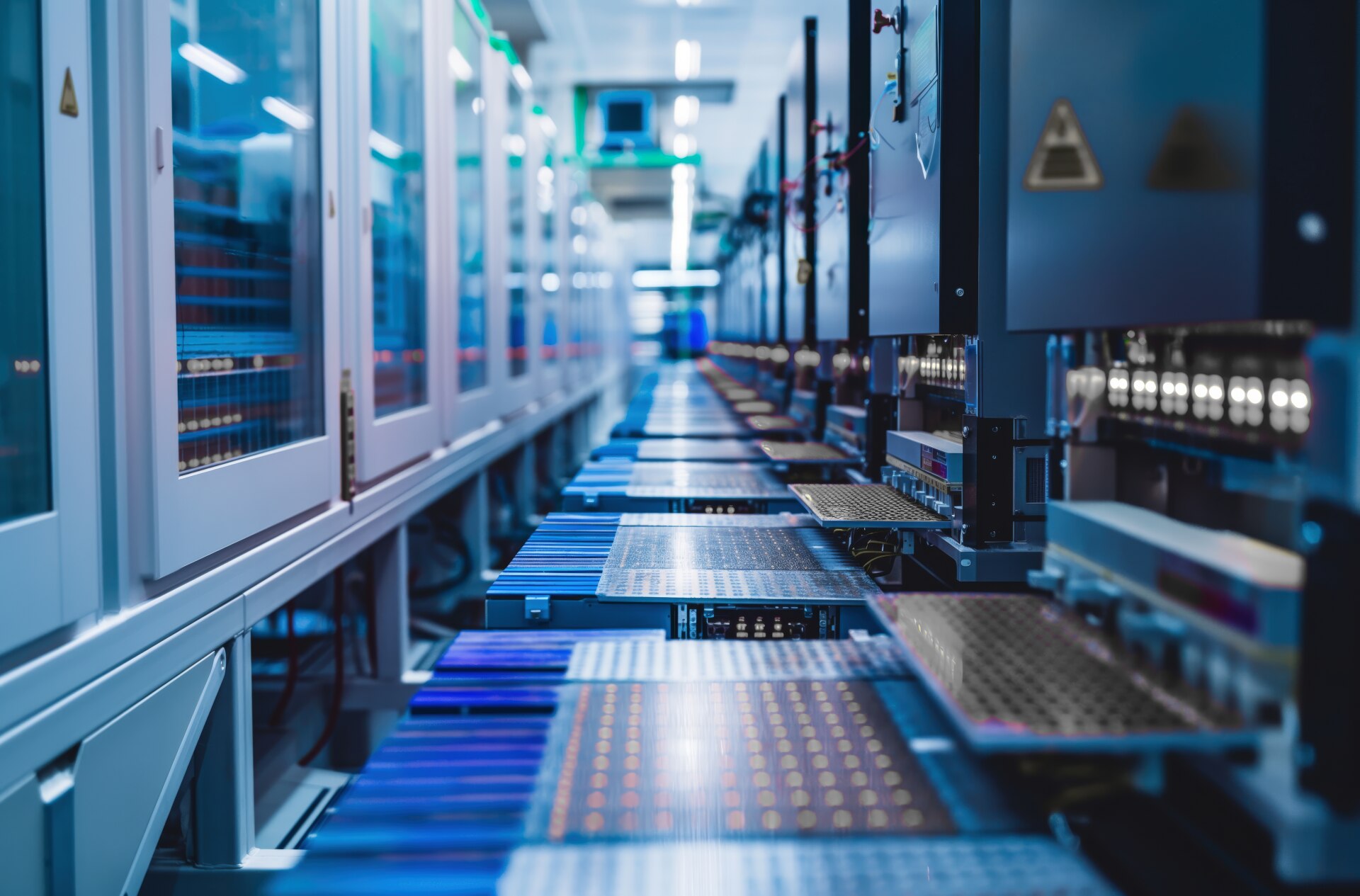
dfx
Design for Excellence
The NPI therefore stands for Design for ExcellenceThis definition was developed in collaboration with the ZVEI in the "Service in EMS" initiative. The DFX includes 3 stages, which are divided into product definition, material and supplier selection in cooperation with our purchasing department and prototype construction.
In the area of product definition, two important things are in the foreground. Firstly, the Design for testability (DfT) and the Design for Manufacturing (DfM). This means that risk is minimised right from the start, as both the test concepts and the production specifications are designed close to series production.
The material and supplier selection is divided into the areas of Design for Cost (DfC) and Design for Logistics (DfL). Under these premises, our specialists from the NPI and purchasing department work very closely together to achieve the best possible result. Here, care is taken to ensure that the required materials are available and that they can be supplied reliably. A cost-benefit analysis is also carried out and cost transparency is maintained.
The DfX concludes with prototype construction. The first samples are manufactured in a near-series production environment and the testing and production concept is verified. The readiness for series production is tested here in close cooperation with development.
The classic mechanisms of the integrated logistics concept then come into play via the supply chain and the structure of the production line. In the end, you receive your product in tested quality, on time and in the required quantity.